- Home »
- Learningcenter »
- Way re roof warehouse
The Right and Wrong Way to Re-Roof a Warehouse
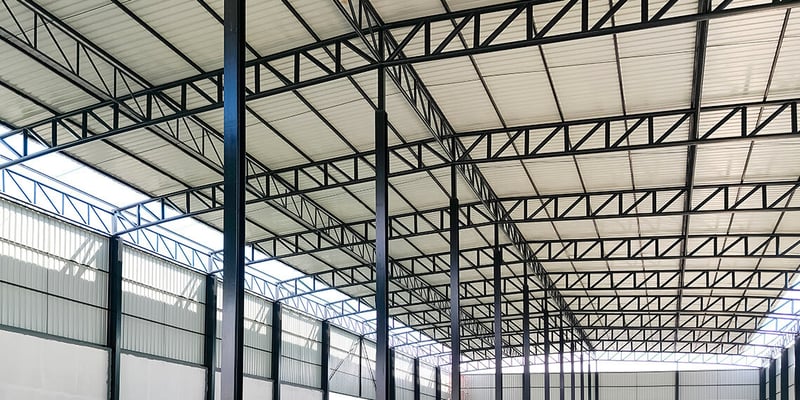
People who make the mistake of ignoring roof maintenance can end up paying thousands in surprise costs. Roofing companies really are in charge of making sure the building stays usable, safe, and durable. So, roof problems like aging, leaks, and needing better energy efficiency can all show up. Because of this, it makes re-roofing a big and sometimes a bit scary job for you business owners or maintenance managers. It also makes it very important to pick the right roofing partner (like us at Colony Roofers!)
When you install a new roof the right way, it can actually help with the safety and performance of the whole place. You'll also sometimes stay away from expensive mistakes and make your roof last a bit longer.
If you want to know more, just keep reading!
Why Is Planning Important?
When starting a re-roofing project for your warehouse, you need to plan wisely. Thoughtful planning will save you time, money, and stress - and you'll feel more in control.
First, you should think about what type of roofing material to use. You have options like asphalt shingles, metal roofing, tiles, and slate. All these choices vary in cost, durability, and appeal, so pick what fits your budget and needs. The right choice will stay around that your warehouse survives whatever Mother Nature throws at it and goes hand in hand with your budget.
Be sure to always keep your budget in mind, too. Talk to your contractor about your budget and timeline - this helps them create a plan that's affordable and quick. A clear financial picture opens new options and keeps disruptions to a minimum. Then your warehouse operations won't suffer as much if everything's planned out.
Never ignore permits and local rules. Know your local building codes and the needed permits to stay compliant - this keeps you safe and in line with construction standards. Just imagine how frustrating it would be if your project got stopped because you ignored paperwork - it can be an avoidable delay.
Safety steps are important and they protect your crew and warehouse property. Keep talking with your contractor - this way any changes or issues can be fixed faster. An easy conversation can stay away from big problems. Once, a customer's project got stalled because the roofing company never discussed material delivery with them! You don't want that to happen to you.
Always think about your neighbors and let them know about the re-roofing project. Also, protect loose items and your landscaping to keep things smooth. Make sure there's a clear path for workers and equipment - this keeps the job running without any obstacles.
It's good to take a look at logistics and timing. Coordinate the delivery of roofing supplies and dumpsters, and plan replacement dates to stay away from inconvenience. Sometimes there could be temporary effects on parking or loading docks, so plan for those too - this minimizes disruptions for everyone.
So, create a complete timeline and checklist. Include milestones for material delivery, permits, and installation days. A checklist helps you catch small details like insurance and neighborhood notifications. When you cover all bases, you'll ensure that nothing gets missed and keep the project on track.
But re-roofing your warehouse isn't easy, but with good planning, it's manageable. You'll steer clear of potential dangers, you can use your resources well, and get everyone on the same page. Honestly, planning will make this big job less stressful and more achievable!
Choosing the Right Roofing Material
When you're picking roofing parts for your warehouse, you have options like metal, TPO, and EPDM. Metal roofs made from steel, aluminum, and zinc can last 40-80 years. You'll get excellent durability because they stand up to heavy rain, hail, and high winds. Their ability to reflect solar heat can also help cut cooling costs. You'll find metal roofs are non-combustible and have recycled parts, but installation costs more, and they can be noisy during heavy rain and hail.
Maybe you could choose TPO roofs if you want toughness and affordability. But they resist peeling and cracking, and algae and mildew don't grow on them. Their reflective properties can really lower cooling costs in hot areas. You do need to bond them to create seams - which is something you should keep in mind.
Also, you should think about EPDM roofs for high resistance to weathering and UV damage, and they prove to be tough and long-term. You'll find them lightweight and easy to install, but they can tear and puncture, needing skilled labor for installation.
Climate matters when picking parts. Warehouses along the coast could benefit from aluminum metal roofs because of high corrosion resistance. In hot climates, TPO roofs can really cut energy costs. Also, industrial areas benefit from EPDM because of its resistance to chemicals and saline water. The choice of material really affects the warehouse's efficiency and maintenance needs.
Look at real-life examples for plans, too. Warehouses in hurricane-open areas sometimes use metal roofs for their sturdiness. Sunny regions like TPO roofs to reduce cooling costs. Also, industrial zones could use EPDM for its chemical resistance. These choices give you helpful services for specific environmental challenges.
Always think about the long-term implications, too. When you pick the right material, you'll save on repairs and reduce the need for regular maintenance. Energy-efficient parts like metal and TPO lower energy bills over time. The correct material set also minimizes maintenance and helps keep your roof in good shape. Fire-resistant parts help with safety in high-danger areas - long-term planning helps maintain the building's integrity and cuts back on costs.
Always factor in details like roof pitch, budget, and the local climate. Low-slope roofs sometimes need specific parts like TPO or EPDM. Your budget can also change what you choose. Analyze the lifespan of each material - steel roofs can last over 50 years, while asphalt shingles last 15-30 years. Remember to check local building codes and regulations to stay around you comply - learning about the rules can save you trouble.
Use these points when picking on roofing for your warehouse. The right roof can mean lower costs and better toughness. When you invest time now, you'll make the smart choice for the future!
What Are the Safety Measures?
When you re-roof a warehouse, start with safety first. Be sure to make sure everyone stays safe with important safety practices. Don't underestimate how big a deal it is to follow local safety rules and codes. Sometimes accidents happen because people fail to follow these guidelines - so take this really!
Always wear the right personal protective equipment (PPE). First, put on hard hats and safety glasses - then add work gloves and high-visibility clothing. Never miss an opportunity to wear safety toe boots and respirators. Even though these basic items could feel small, they could save you from a trip to the hospital. Personal fall arrest systems are also important for your safety. You don't want the pain of dealing with a fall.
Next, you should think about fall protection, too. You should set up perimeter flag lines and safety rails to help stop falls from the roof's edge. Actually, guardrails, safety nets, and personal fall arrest systems add extra security. Also, you should check your ladder. Does it feel stable and protected? Make sure it follows OSHA standards to stay away from accidents.
Remember to manage access and debris. Plan roof access with ladders, scaffolds, or boom lifts for safety. Nobody likes tripping over loose parts. A clean workspace lowers the danger of slips and falls.
Most, remember electrical safety. Run regular electrical safety checks to stay away from electrocution. Also, power lines and electrical hazards on rooftops are real threats. Always stay away from them and use non-metal ladders nearby. You'll be grateful for your caution.
Also, watch the weather. Stay indoors during heavy rain, strong winds, or extreme heat. It's an easy tip, but people sometimes ignore it. You should keep your team hydrated - especially in hot weather. After all, a hydrated team works more safely.
Always handle hazardous parts with care. Especially watch out for asbestos and paint fumes, which can be dangerous. When you are placing and handling these parts, doing it the right way is a must. Adequate training on how to manage these substances can save your life.
Make sure to always cover skylights and roof openings securely. Make sure covers can hold at least twice the weight of workers, parts, and equipment. You don't want to find out too late that the cover wasn't strong enough.
Regular safety checks and training sessions are helpful. These practices keep everyone aware of potential dangers. Actually, good communication among workers keeps safety at the front. When everyone is alert, accidents happen less.
Did you know falls make up 20% of construction deaths and 84% of roofer fatalities? Really, roofing is one of the top three most deadly jobs in the U.S. - falls cause injuries or deaths. Most of these incidents can be prevented with strict safety measures.
Safety measures save lives!
Engaging Skilled Professionals Matters
You need to hire skilled pros for a re-roofing job. You could think anyone with basic tools can just handle it - but it's actually quite a bit more complicated. Experts are best in areas like insulation and ventilation. Sadly, incorrect installation can really create serious moisture problems and shorten your roof's lifespan - this can cause higher energy costs! You really don't want these kinds of issues, believe me.
You have to think about safety, too. Professional roofers stay safe with special safety gear - like fall arrest systems and personal protective equipment. Just imagine trying to get through a steep roof without training or the right gear. It's a disaster waiting to happen! Skilled roofers also place and fix small issues before they turn into big problems - this can actually save you lots of headaches in the future.
You can't ignore the quality and reliability you'll get with pros. Experienced roofers know exactly which products and techniques are reliable for long-term durability. I've seen jobs where unskilled people cut corners and caused a bunch of problems later.
When you do anything less, it's just too risky.
I remember hearing about a warehouse project that went south because the contractor didn't install the insulation the right way - this caused extreme moisture buildup - and the whole roof had to be redone. When you hire a seasoned contractor, they will actually make sure that everything is up to standard. From insulation to ventilation, every part will be done right. You see the difference it makes, don't you?
You always have to find and vet the right contractor. Start by looking at their experience and certifications. A reliable contractor will have lots of experience (especially in commercial roofing), and they will also have the right certifications that show their expertise. Remember to read reviews and ask for references - what past clients say can give you real insight into their reliability and workmanship.
Don't be shy to ask potential contractors about their safety protocols and gear. When you judge their commitment to safety, it can save you trouble. Always get multiple quotes to compare services and prices - make sure each quote details the work. When you talk to contractors, just take a look at their professionalism and attitude. A positive attitude and strong work ethic mean you've likely found the right team.
When you hire skilled pros, your re-roofing affects the quality of the job, safety, efficiency, and long-term maintenance of your warehouse. It's honestly a sure-fire way to stay away from unnecessary headaches - maintain good quality and get the job done right the first time. Why gamble with anything less?
How to Handle Unexpected Issues?
You know how unexpected issues can turn an easy re-roofing project into a real headache. Bad weather, structural problems, and flawed insulation sometimes cause the most trouble. Let's jump right into how you can deal with these problems.
You can't control the weather but you can schedule the work during a favorable season. Sometimes bad weather interrupts your plans. Rain, snow, and extreme temperatures cause delays. Rain can soak your roof's decking and freezing temperatures can interfere with material integrity. Keep your project timeline flexible and make sure your roof is dry before you lay any new material. So, you don't want a soaked deck halfway through the job!
Sometimes structural problems bring unpleasant surprises. Rotten rafters and worn-out flashing can show up during re-roofing. You should do a complete inspection before you start and order any needed parts in advance. If your rafters are bad, you'll stop progress cold. When you find these issues ahead of time, it saves you frustration and cash.
Flawed insulation throws another curve ball at you. Rotten underlayment or thin decking sometimes go unnoticed until you start tearing things apart. A complete inspection helps expose these issues before they become serious problems. So, replace any bad parts before moving forward. It feels much better to start with these problems initially instead of dealing with them later.
You know preparation is important in these scenarios. Set up a contingency plan and add some padding to your budget. Try to set a flexible timeline and reserve funds for unexpected issues. Because getting caught off guard without extra cash can spell disaster. When you have extra funds on hand, it turns a potential crisis into another small bump in the road.
Communicating closely with your contractor is very helpful. A licensed, experienced roofer works with unforeseen issues well, and they also help with insurance claims, which will make sure that the job's done right the first time.
You should keep a complete record of all activities, costs, and communications because this helps you with insurance claims or future references. Complete records make everything easier and help avoid confusion later. It will show that you're prepared for any situation!
Protect The Roof Over Your Head
When you think it over, you'll see that re-roofing a warehouse isn't very easy. You need to plan and pick the right parts. You also must follow safety guidelines and get a team of certified pros for the job - this way, your re-roofing will be smooth and successful! What challenges have come up in your own roofing projects? Have you found any tricks that actually made things easier? You know, personal stories sometimes show some of the best tips and hidden strategies - don't they?
In these cases, hiring skilled pros is really helpful. A seasoned contractor helps you manage safety and pick the right parts. It's sort of like when you have a helpful guide through the difficult world of roofing. Would you choose to save money now or ensure your roof lasts a long time? Roofs are one of those projects that you want to get done right the first time.
Here at Colony Roofers, we handle commercial and home roofing. Based in Georgia, Florida, and Texas - we're ready to take care of your roofing needs. Trust us to keep your investment and safety in good hands. Whenever needed, reach out for a free inspection, and we'll give your roof the care it deserves.
When uncertain, you should always ask a trusted roofing professional like Colony Roofers. We have expert advice and quality repair and installation services. So, contact us today!