- Home »
- Learningcenter »
- Atlanta roof access osha
What Are The Atlanta Roof Access and OSHA Compliance Rules?
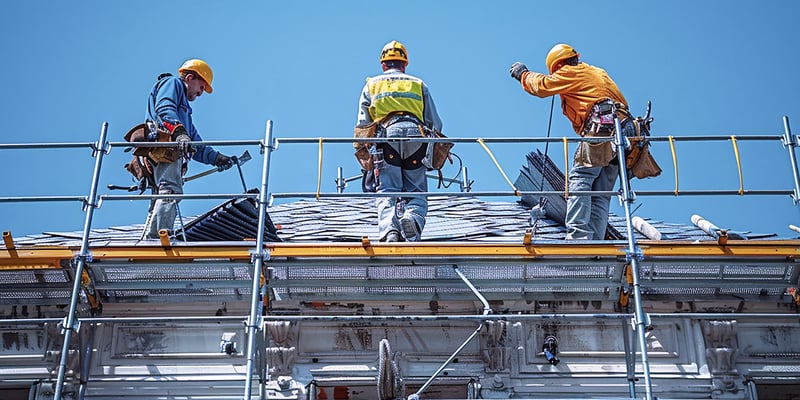
Atlanta property owners and contractors have to handle many different safety regulations that can hurt their business if they ignore them. For rooftops, you're actually dealing with two different sets of regulations for the same space. The city follows local building codes. But they also have to follow federal OSHA standards, and these two systems work together to create some pretty tough safety requirements for anyone who needs to get up on a roof.
Every single day, workers climb up onto rooftops to work on HVAC systems and fix equipment. Their families are at home waiting for them to come back safely. After a few workplace accidents happened recently, Atlanta started paying much more attention to rooftop safety. Now they're doing stricter enforcement and charging higher penalties when people break the laws.
Today, if you get caught breaking safety laws, you're going to pay much bigger fines, and this goes for all types of commercial properties. Your business has direct liability whenever something goes wrong during routine maintenance work. The compliance teams are doing inspections more often now, all around the metro area.
Let me talk about how these two sets of regulations work for your business and the specific steps you need to take to stay on the right side of the law.
Atlanta's Building Codes for Roof Access
Atlanta takes roof safety very seriously, and the city has standards in place that go beyond what federal OSHA requires. The city created these stricter standards after looking at just how many tall buildings and tight spaces we have here in Atlanta. Most contractors find out about this difference when they start working on their first project in the area. With that much urban density, workers need extra protection whenever they're up there servicing rooftop equipment.
The most critical law to know about involves permanent ladders. If equipment sits more than 30 inches above the roof surface, Atlanta mandates installing a permanent ladder for servicing. This isn't optional - it's written right into the city's building code. If you skip this requirement, you're putting your workers in danger, and the business could end up in legal problems. Atlanta inspectors treat ladder violations as safety problems. Maintenance crews need to have safe access to equipment, and they shouldn't have to come up with dangerous workarounds on their own.
Atlanta also has particular requirements for guardrails that exceed what you'll see in other cities. The city says that guardrails have to be 42 inches high when installed around roof access areas. You can't just guess at this measurement either - city inspectors care about getting it right. City inspectors will actually bring out measuring tools to check the height when they come for compliance reviews.
The permit process in Atlanta has gotten more involved in recent years. Before installing any rooftop HVAC equipment, mechanical permits are needed along with the right engineering paperwork. The city wants to make sure that the roof can actually support the weight of the equipment, and workers will be able to safely get to everything when it needs servicing later on. Structural calculations are needed for most installations.
Violation fines start at $500, and they can increase pretty fast if inspectors catch repeat offenses. Keep breaking the law, and you could end up paying thousands of dollars for each incident. When city officials come out for inspections, they focus closely on ladder placement and guardrail heights.
Federal OSHA Rules for Fall Protection
Atlanta's local requirements are just the beginning for roof access compliance. The federal OSHA laws apply across the country and usually take priority over local codes. You need to follow both sets of laws at the same time in most cases. This kind of dual compliance creates extra work. But there's no way around it.
OSHA has what they call a hierarchy of fall protection controls. The first step is getting rid of hazards completely when possible. If you can't get rid of the hazard, then move on to engineering controls like permanent guardrails or safety nets. Personal protective equipment comes last in this hierarchy, but it's still important for most roof work. This hierarchy shapes every safety choice you make on a job site. Some contractors skip straight to harnesses and end up missing safer options that could protect their entire crew. The whole approach makes you think about permanent fixes before relying on personal equipment.
The federal standards just got much stricter, too. Since July 1, 2025, fall protection is needed at just 6 feet above ground level for residential construction work. That's a big change from the previous 15-foot threshold. Most roof access situations now trigger these requirements.
Personal fall arrest systems have specific anchor point requirements under OSHA laws. Each anchor point has to support at least 5,000 pounds per worker attached to it. The equipment itself has to meet the updated ANSI Z359.14-2021 standards, which bring stricter testing and performance criteria for self-retracting devices. Those numbers matter when inspectors show up. OSHA also requires regular inspection and maintenance of all safety equipment. You can't just install a system and forget about it. The employer has to provide the right training and create site-specific safety plans that cover every location's specific hazards.
Equipment that sits unused for months can develop problems that only show up when someone needs it. Once you have training records and maintenance logs, they become proof of your commitment during any regulatory review.
Creative Options for Building Safety Compliance
When a building's standard safety measures don't work the way they should, property owners need to get creative with how they address compliance. Atlanta's building department has significantly stepped up its enforcement over the past year or so, as we talked about earlier. The city isn't going to care about budget constraints or the particular challenges a building faces. They expect property owners to follow safety regulations precisely as written.
This puts owners in a tough position when their building has some unusual features or historic restrictions that make compliance more involved. As a property owner, pressure comes from all different directions. Enforcement officers show up at the door with their clipboards and citation books ready to go. Maintenance budgets suffer while trying to find options that actually work with a building's particular features.
There are customized anchoring systems out there that can solve many of the problems that standard guardrails just can't address. These systems are designed to work around architectural features while still meeting all the OSHA requirements. Buildings might end up needing custom brackets for curved surfaces, or maybe temporary anchor points for short-term projects. Custom options work with the space rather than forcing everything to fit a standard mold.
The reason one-size-fits-all methods don't work is because every single building is different. A historic property downtown needs completely different options than a modern warehouse would. How frequently maintenance crews need to access the roof matters too - if crews head up there every day, the equipment needs differ from buildings where they only head up once a month. These building differences have real consequences when planning for safety. Historic structures usually have protected facades that make it hard to install traditional equipment. Modern buildings could have those membrane roofs that just can't support traditional anchor points. How the roof actually gets used helps determine whether permanent options or temporary ones make more sense.
Working with certified experts who understand the federal OSHA regulations and Atlanta's particular requirements can help with these complex situations. They might recommend modular guardrail systems if permanent changes aren't going to work for a building. Professional input becomes especially valuable when dealing with overlapping regulations.
There are times when aerial lifts make more sense than permanent installations. This holds especially true for buildings where people don't go on the roof very much, or if the building has complex architectural features that make other options difficult. Think through what a building actually needs based on how it's used and maintained. When people go with cheap options, they usually don't pass inspection anyway, and then there's the cost of those citations on top of everything else.
Atlanta Takes a Stricter Safety Approach
Atlanta has seen roof access violations jump by 40% over the past year. Real workplace accidents have made the city start cracking down much harder on safety regulations that people used to ignore all the time.
This whole change came about after a few serious incidents where workers fell from rooftops. These accidents could have been prevented if people had just put basic safety measures in place. The city's taking these violations much more seriously now.
If you look at where most violations happen, it's usually in the same few areas. People either skip fall protection systems completely or they install them incorrectly. Ladder access points don't meet the code requirements they're supposed to, and emergency escape routes either aren't there at all or workers can't get to them safely when they need them.
The city used to mainly try to educate people first. Inspectors would warn property owners about problems and then give them some time to fix whatever was wrong. But that whole approach has changed now. Now you're a lot more likely to get hit with an immediate citation that comes with a big fine. Citations start at $500 for basic violations. If you get caught again, your costs go way up from there. The days of having extra time to make corrections are pretty much gone.
Atlanta's enforcement has become much stricter when you compare it to other southeastern cities like Charlotte or Nashville. While those cities still usually give warnings and try to educate people first, Atlanta has moved straight to writing citations. This puts property owners and contractors in a tough position where they have to get everything right from the beginning.
Most inspections now start because workers complain or because someone gets hurt, and there's an investigation. When someone reports unsafe conditions or gets hurt on the job, inspectors usually show up pretty fast. You just can't wait until there's a problem to address safety issues. After any reported incident, your building immediately goes on the list for inspection. Workers can now go straight to city enforcement through online complaint systems, which makes it much easier for them to report problems.
How Much Will You Pay
The first fines are actually just the beginning of what happens when someone ignores the regulations for roof access. OSHA raised its penalties in January 2025 to make these violations cost much more than they used to - and these aren't small adjustments we're talking about. Say, someone gets hit with a major violation, they're now looking at as much as $16,550 per incident, which is up from the previous $16,131.
If violations continue, those numbers will start to get pretty scary very quickly. When they catch repeat violations, the fines can go all the way to $165,514 per incident. We've already seen Atlanta contractors get hit with six-figure penalties just this year, and some of them are looking at over $300,000 in fines because they didn't have the right fall protection in place. Each violation gets added to the ones before it, and businesses start to get extra attention from inspectors. When OSHA sees repeat offenders, they like to use them as examples to show the rest of the industry what happens when safety requirements are ignored.
But the real damage actually goes further than that first ticket. After OSHA marks a business as a problem, they're going to start looking at every single safety program in place, which means they'll be checking everything. Usually, the local authorities will also start showing up for their own inspections, which means even more opportunities for them to find problems. Insurance companies are going to find out about these violations, and they'll raise premiums because of it.
When there's a track record of safety violations, worker compensation claims are going to become much more expensive. If someone ends up hurt on a job site, those previous violations are going to make it much harder to mount a legal defense. People in the construction community talk to one another all the time, and once word gets out about a contractor who cuts corners on safety, it can take years to rebuild that reputation. The legal fees alone can get out of control when defending against multiple claims at once. Insurance providers will see the risk as too high to provide affordable coverage.
After violations go on record, it gets much harder to secure the permits and licenses needed for future projects. There are some clients out there who won't even think about hiring contractors who have received OSHA penalties recently. If someone becomes a repeat offender, OSHA might require hiring safety consultants, or they might come to review sites much more often than they normally would. When trying to bid on new projects, competing against contractors with clean records becomes harder. Profit margins will get smaller and smaller as more money goes toward staying in compliance.
Follow the Rules for Roof Safety
When businesses understand both Atlanta's local building codes and federal OSHA standards, they create a safety framework that keeps workers safe while making sure the company follows the law. These two sets of regulations actually complement one another nicely - Atlanta's extra requirements build on top of what OSHA already gives you. Business owners who actually know what they're doing see compliance as a smart investment in their workers and their company's future stability.
The regulations keep changing as safety experts learn new information about preventing workplace accidents and as better technology becomes available. These updates happen every few months or so, which means keeping up with compliance isn't something you do once and forget about - companies need to keep checking and updating their policies regularly. Schedule a compliance audit or review existing roof access systems against the latest standards to avoid expensive violations and, more importantly, prevent serious injuries to workers.
Getting roof access systems to meet standards takes time and money at the start. But the dangers of not doing it are much bigger for everyone involved. Workplace accidents can cause terrible injuries, big legal problems, and damage to a company's reputation that can take years to recover from.
Just one workplace injury can cost your business hundreds of thousands of dollars in legal fees by itself. Insurance costs skyrocket after safety violations and stay high for years. Workers will start looking for other jobs when they don't feel safe at work. Workers' compensation claims leave a paper trail that follows companies when they're trying to land new contracts.
At Colony Roofers, we work on commercial and residential roofing, and we have offices in Georgia, Florida, and Texas. Contact us for a free inspection, and we'll take care of your roof properly. We provide expert advice and take care of all repair and installation needs. Get in touch today!